You signed in with another tab or window. Reload to refresh your session.You signed out in another tab or window. Reload to refresh your session.You switched accounts on another tab or window. Reload to refresh your session.Dismiss alert
I have noted that many ppl show broken 3D printed parts of tourniquet. Reason for that - wrong slicing settings, wrong nozzle dia, low nozzle temperature and high cooling settings. Also wet plastic could become a big problem here.
I have used PETG with 245 degrees 0.6 mm nozzle and smallest rpm (35%) of cooling for just to remove stringing.
For slicing, main point for high loaded parts is to have as long non "retracted" line. So you want to avoid as much as possible retractions at load points.
Here is example of bad slicing, seam is right in weakest place of windlass:
To resolve it, pick different setting for seam location, like "Random" or better "Sharpest corner", that way all retraction will be at non critical places.
The text was updated successfully, but these errors were encountered:
I have noted that many ppl show broken 3D printed parts of tourniquet. Reason for that - wrong slicing settings, wrong nozzle dia, low nozzle temperature and high cooling settings. Also wet plastic could become a big problem here.
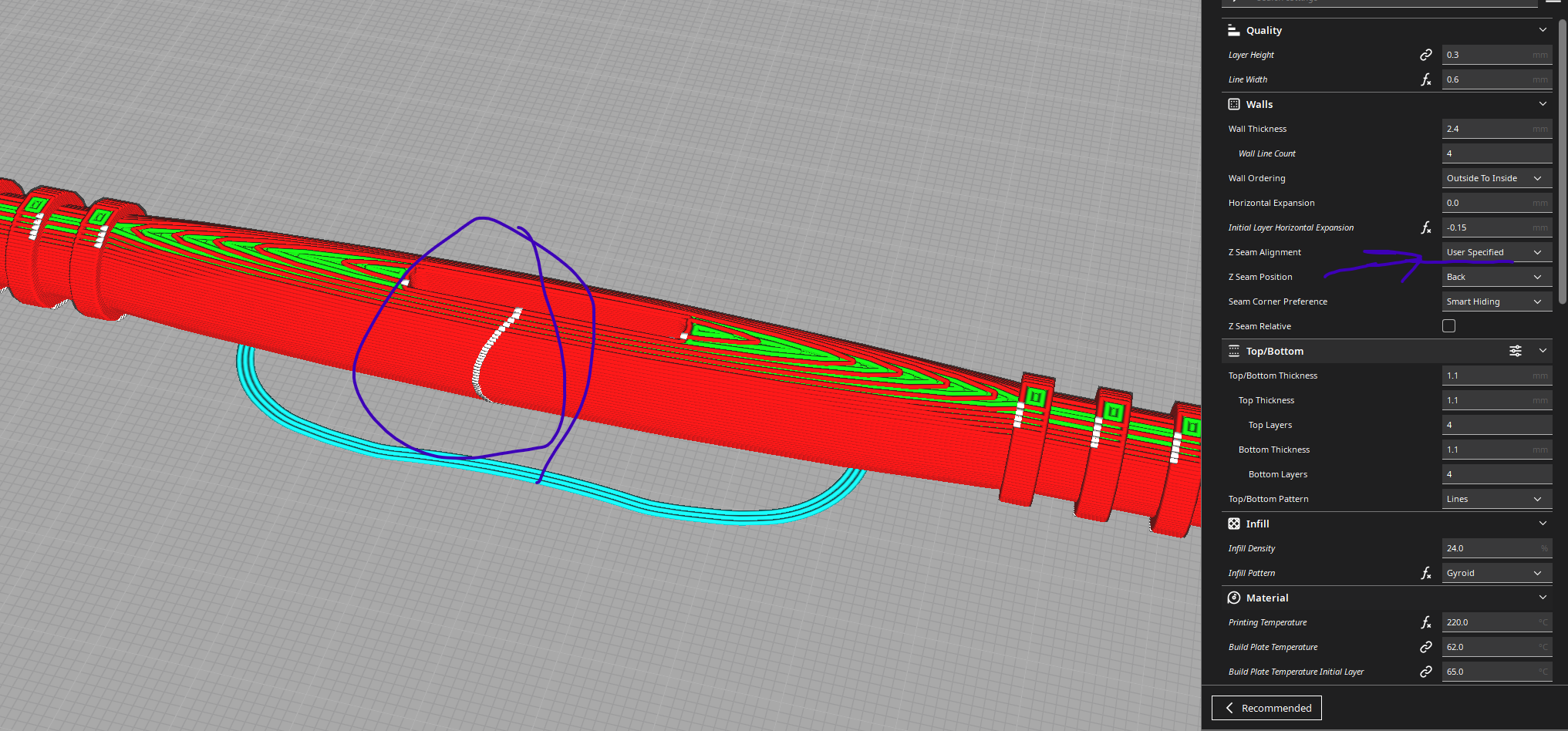
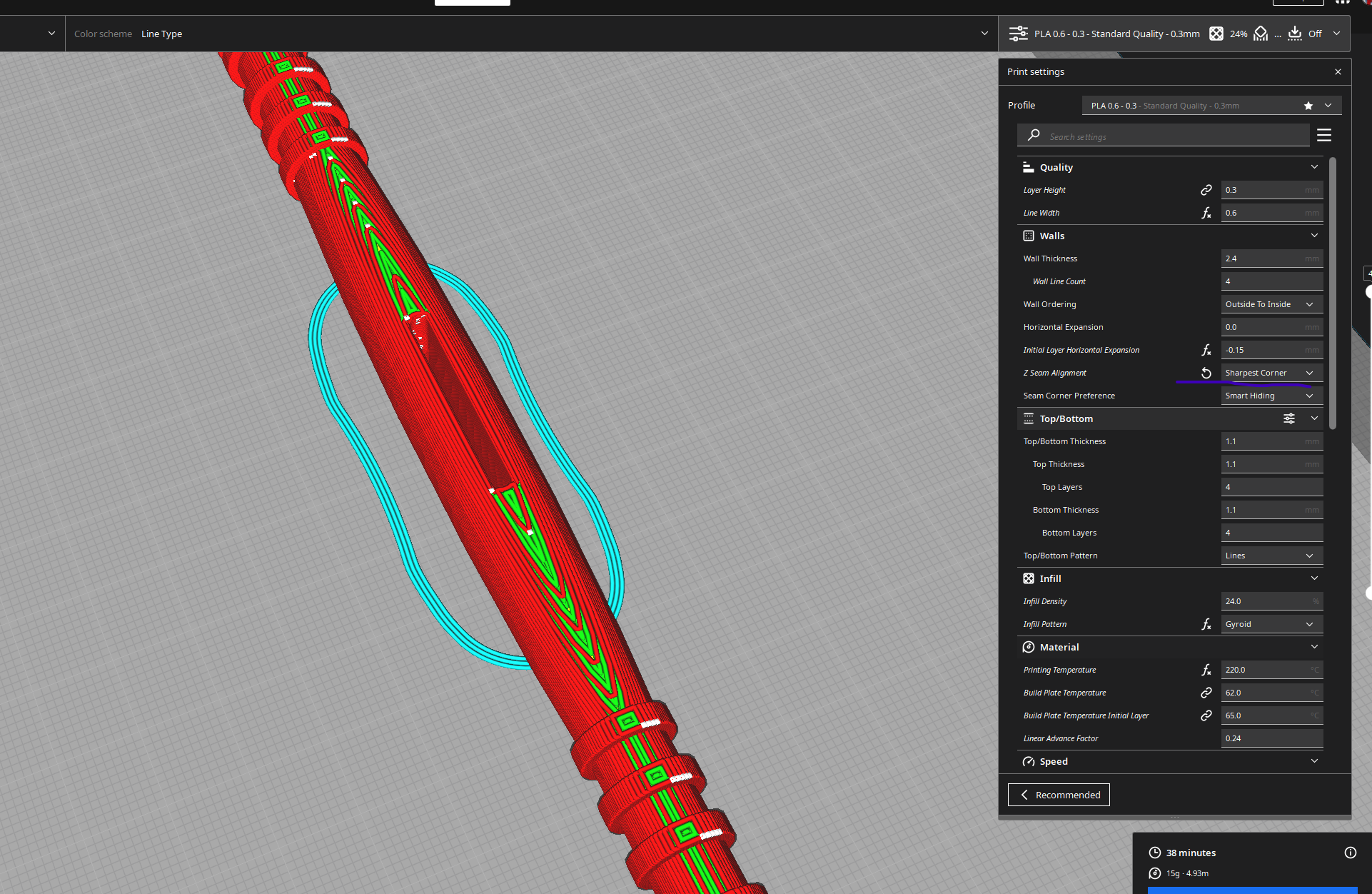
I have used PETG with 245 degrees 0.6 mm nozzle and smallest rpm (35%) of cooling for just to remove stringing.
For slicing, main point for high loaded parts is to have as long non "retracted" line. So you want to avoid as much as possible retractions at load points.
Here is example of bad slicing, seam is right in weakest place of windlass:
To resolve it, pick different setting for seam location, like "Random" or better "Sharpest corner", that way all retraction will be at non critical places.
The text was updated successfully, but these errors were encountered: